Understanding the Manifold Valve Working
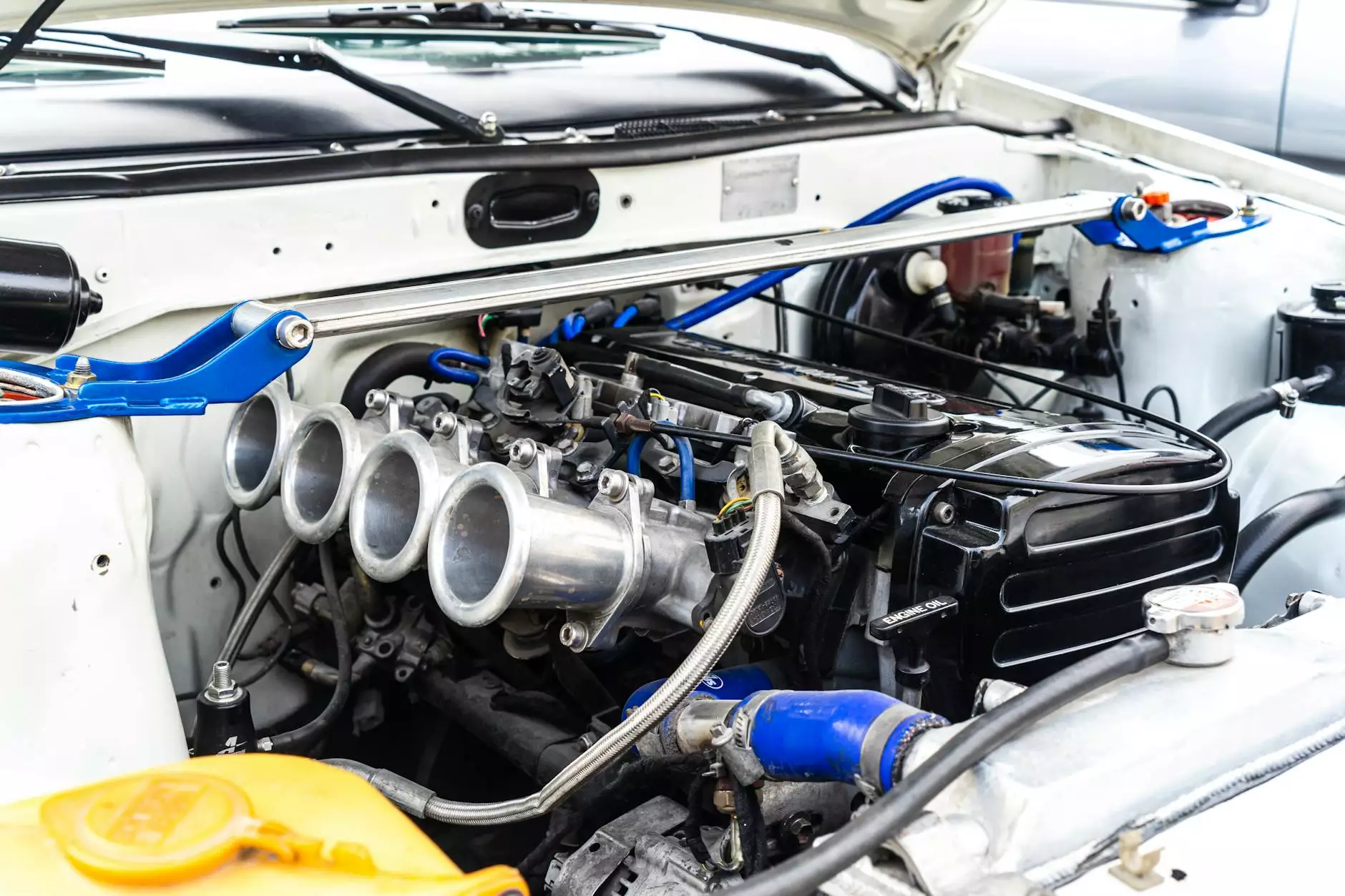
The manifold valve working is an essential aspect of fluid dynamics in various industrial applications. Manifold valves play a critical role in controlling the flow and distribution of fluids in hydraulic and pneumatic systems. This article will delve into the workings of manifold valves, their functions, types, and applications across different industries.
What is a Manifold Valve?
A manifold valve is a mechanical device that channels and regulates the flow of fluids within a system. It serves as a control system that allows the user to manage several operational aspects using a single valve body. Manifold valves are particularly common in hydraulic and pneumatic systems, where they assist in optimizing performance and functionality.
How Do Manifold Valves Work?
Understanding the manifold valve working principle requires a look at its components and the flow control mechanism:
- Body: The main structure that houses the valve mechanism and connections.
- Ports: Inlets and outlets through which fluids enter and exit the valve.
- Control Elements: These include spools or discs that can move to either obstruct or allow flow.
- Actuation Mechanism: Manifold valves can be operated manually or automatically through electrical signals.
When fluid enters the manifold valve through one of the ports, the internal control elements determine how the fluid is channeled. Depending on the design, the valve can divert the fluid to multiple outputs or sequentially control which output receives the flow. This flexibility is crucial for applications that need precise pressure management, such as hydraulic lifts, industrial machinery, and automotive systems.
Types of Manifold Valves
There are several types of manifold valves, each designed for specific applications:
1. Hydraulic Manifold Valves
Hydraulic manifold valves manage the flow of hydraulic fluids, ensuring that pressure and flow direction are appropriately controlled in hydraulic systems.
2. Pneumatic Manifold Valves
Similar to hydraulic valves, pneumatic manifold valves control the flow of compressed air and gases in pneumatic systems, optimizing air distribution for automated processes.
3. Multi-ports Manifold Valves
These valves feature multiple ports for simultaneous control of several lines, allowing for intricate setups in complex systems.
The Advantages of Using Manifold Valves
The incorporation of manifold valves significantly enhances system performance and reliability. Below are some notable advantages:
- Space Efficiency: Consolidating several valves into one manifold can save valuable space in machinery and pipelines.
- Cost-Effectiveness: Fewer components mean reduced costs for maintenance and installation.
- Improved Safety: Centralized control allows for more straightforward monitoring and management of fluid systems.
- Enhanced Performance: Manifold valves can improve flow control, ensuring optimal functioning of hydraulic and pneumatic systems.
Applications of Manifold Valves
Given their versatile nature, manifold valves find applications in various industries:
1. Automotive Industry
In the automotive sector, manifold valves are crucial for controlling hydraulic brake systems and power steering, ensuring safety and efficiency in vehicle operation.
2. Manufacturing and Robotics
Manufacturing plants utilize manifold valves in pneumatic systems for robotic automation, improving workflow efficiency and productivity.
3. Oil and Gas
In oil and gas extraction, manifold valves facilitate the control of fluids and gases, which is critical for maintaining safety and efficiency during extraction operations.
4. Aerospace
The aerospace industry relies on manifold valves for hydraulic and fuel systems, where precision and reliability are paramount.
5. Marine Applications
In marine environments, manifold valves are utilized for controlling various fluids on ships, enhancing operational safety and performance.
Installation and Maintenance of Manifold Valves
Proper installation and maintenance of manifold valves are crucial for their performance and longevity. Below are some key steps to consider:
Installation Guidelines
- Ensure that the valve assembly is compatible with the existing system specifications.
- Follow manufacturer guidelines for proper alignment and connection to prevent leaks.
- Check for proper pressure ratings to avoid system failures.
Maintenance Practices
- Regularly inspect the manifold for signs of wear, corrosion, or leaks.
- Clean the valve and surrounding components regularly to prevent buildup that can affect performance.
- Ensure that all seals and connections are tight and free of debris.
Conclusion
Understanding the manifold valve working principle is essential for anyone involved in industries that rely on fluid dynamics. From their design and functionality to their applications and advantages, manifold valves provide significant benefits that enhance system efficiencies. By prioritizing proper installation and regular maintenance, industries can leverage the full capabilities of manifold valves, ensuring reliable and efficient operations.
For those interested in exploring manifold valves or understanding more about their applications, feel free to reach out for further information. At TechTubes.in, we offer a comprehensive range of products related to tube fittings, ferrule fittings, forged pipe fittings, threaded pipe fittings, flanges, and more, ensuring you have access to the highest quality components for your systems.