The Essential Guide to Injection Moulding Tooling for Metal Fabricators
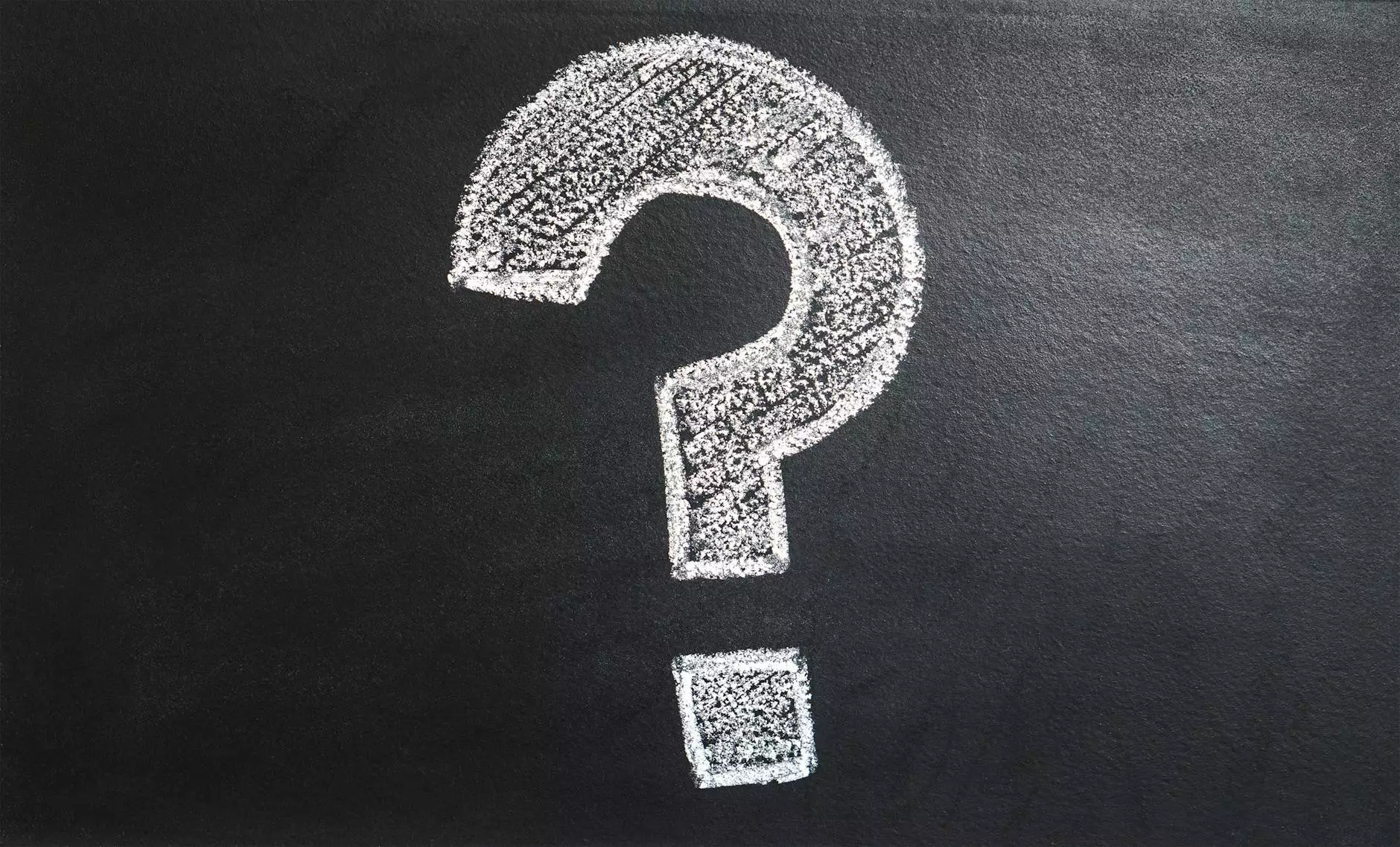
In today’s competitive manufacturing landscape, injection moulding tooling stands out as a vital technique that numerous businesses, especially in the realm of metal fabrication, adopt for their operations. This article will delve into the intricate world of injection moulding tooling, outlining its processes, benefits, and best practices, ensuring that companies like deepmould.net secure their place as leaders in metal fabrication.
Understanding Injection Moulding Tooling
Injection moulding tooling refers to the creation of molds used to shape and form materials, particularly thermoplastics and sometimes metals, into desired designs. This manufacturing technique is conducive to producing high volumes of identical parts and components quickly and efficiently, making it an indispensable part of the metal fabrication process.
How Injection Moulding Works
The injection moulding process involves several steps, including:
- Material Selection: The process begins with choosing the appropriate material, typically a thermoplastic resin.
- Melting the Material: The selected resin is heated until it melts into a viscous state, making it ready for injection.
- Injection: The molten material is injected into a precision-engineered mold.
- Cooling: Once the material fills the mold, it is allowed to cool, hardening into the desired shape.
- Mold Opening and Ejection: The mold is opened, and the finished product is ejected.
Benefits of Injection Moulding Tooling
For metal fabricators, utilizing injection moulding tooling provides numerous advantages. Here are some key benefits:
- Cost Efficiency: High-volume production leads to significant economic benefits, reducing the cost per part.
- Precision and Consistency: Injection moulding enables the creation of highly detailed and consistent parts.
- Material Versatility: A wide array of materials can be used, allowing for greater innovation in product design.
- Reduced Waste: The precision of the process minimizes material wastage compared to other manufacturing methods.
- Complex Geometries: Moulds can be designed to create intricate shapes that are difficult to achieve with traditional machining techniques.
Key Components of Injection Moulding Tooling
Understanding the components involved in injection moulding tooling is essential for successful implementation:
1. Molds
The most critical part of the injection moulding process is the mold itself. Typically made from steel or aluminum, molds are custom-designed to form specific parts. Their design intricacies can significantly impact the efficiency and quality of production.
2. Injection Unit
The injection unit is responsible for heating and injecting the molten material into the mold. It consists of a hopper for loading materials, a barrel for melting, and a screw for injecting.
3. Clamping Unit
The clamping unit holds the mold in place during the injection process, ensuring that the material fills the mold correctly without leakage.
Choosing the Right Injection Moulding Tooling
When selecting injection moulding tooling, several factors must be considered to ensure optimal results:
1. Material Compatibility
Ensure that the selected mold material is compatible with the type of resin being used. Different materials have different characteristics, affecting the strength and durability of the final product.
2. Design Considerations
The design of the mold is crucial. It should include features such as cooling channels, gating systems, and vents, which enhance product quality and reduce cycle times.
3. Production Volume
The anticipated production volume can dictate the choice of tooling materials and mold design. High-volume production typically requires more robust tooling to withstand the wear and tear of the manufacturing process.
Injection Moulding Tooling Maintenance
Proper maintenance of injection moulding tooling is essential for longevity and effectiveness. Here are best practices:
- Regular inspections: Conduct routine checks on molds to identify and address wear and tear promptly.
- Cleaning: Keep molds free from residue and contaminants that may affect the quality of production.
- Lubrication: Apply appropriate lubricants to moving parts to reduce friction and wear.
- Documentation: Maintain a maintenance log to track repairs and improvements.
Advanced Techniques in Injection Moulding Tooling
With the evolution of technology, several advanced techniques have emerged in injection moulding tooling that can further enhance production capabilities:
1. 3D Printing of Moulds
3D printing is revolutionizing the way molds are created, allowing for rapid prototyping and complex design capabilities that were previously unattainable.
2. Multi-Material Injection Moulding
This technique enables the injection of multiple materials in one cycle, creating components that combine different properties and functionalities.
3. Smart Mould Technology
Integrating sensors within molds provides real-time data on temperature and pressure, allowing for better control and optimization of the injection moulding process.
Future Trends in Injection Moulding Tooling
The future of injection moulding tooling is promising, with trends such as:
- Sustainability: Increasing focus on eco-friendly materials and reducing waste continues to drive innovations in the industry.
- Automation: Advances in automation technologies are streamlining operations and improving efficiency.
- Industry 4.0: The integration of IoT and AI within production lines for predictive maintenance and process optimization.
Conclusion
Injection moulding tooling is a fundamental technique for modern metal fabricators, enabling efficient production, cost savings, and high-quality output. By understanding its intricacies, benefits, and future trends, companies can effectively harness its power to stay competitive in the ever-evolving manufacturing landscape.
For those looking to delve deeper into injection moulding tooling and explore innovative solutions, deepmould.net stands as a pivotal resource, offering advanced tooling solutions tailored to the unique needs of your business.