Understanding Alloy Steel Instrumentation Ball Valves
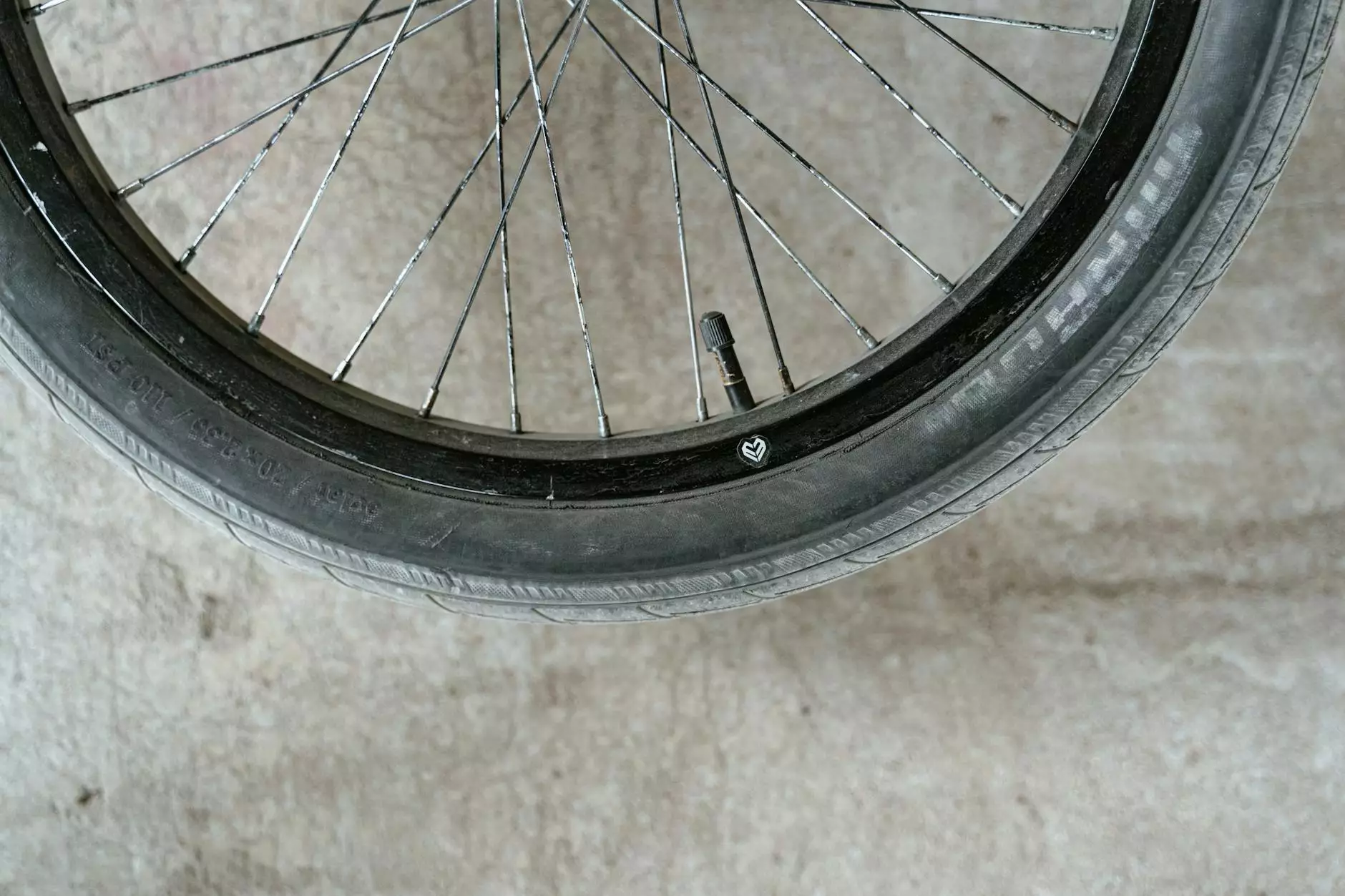
In the realm of industrial components, the alloy steel instrumentation ball valve stands out as a pivotal device that facilitates the smooth operation of numerous systems. These valves are characterized by their robust construction, excellent resistance to extreme conditions, and remarkable performance in controlling fluid flow. In this article, we will delve into the insights surrounding these essential components, exploring their functionalities, advantages, and key applications across various industries.
What is an Alloy Steel Instrumentation Ball Valve?
An alloy steel instrumentation ball valve is a type of valve that utilizes a spherical ball to regulate the flow of fluids. Typically crafted from high-quality alloy steel, these valves are designed to withstand significant pressures and temperatures, making them ideal for use in instrumentation applications. The ball in the valve rotates within the valve body to either obstruct or allow fluid passage, providing both precise control and high sealing capability.
Benefits of Using Alloy Steel Instrumentation Ball Valves
When it comes to choosing valves for industrial applications, the benefits of using alloy steel instrumentation ball valves are numerous:
- Durability: Alloy steel is inherently stronger than many other materials, which means these valves can endure harsh environments.
- Corrosion Resistance: The alloys used in these valves provide excellent resistance against corrosion, making them suitable for use in chemical and petrochemical industries.
- High-Temperature Capability: Alloy steel valves can operate efficiently at elevated temperatures, ensuring reliability in high-heat applications.
- Precision Flow Control: The design allows for precise modulation of the flow, which is crucial in instrumentation applications.
- Quick Operation: The quarter-turn operation offers faster response times compared to other valve types, enhancing operational efficiency.
Applications of Alloy Steel Instrumentation Ball Valves
The versatility of the alloy steel instrumentation ball valve makes it suitable for a range of applications across various industries. Here are some prominent areas where these valves are widely used:
1. Oil and Gas Industry
In the oil and gas sector, these valves are critical for controlling the flow of crude oil, natural gas, and various petroleum products. They are utilized in pipelines, refineries, and storage facilities to ensure safe and efficient operations.
2. Chemical Processing
Given their ability to withstand corrosive substances, alloy steel instrumentation ball valves are commonly employed in chemical processing plants. These valves help manage the flow of hazardous chemicals, ensuring safety and compliance with stringent regulatory standards.
3. Water Treatment Facilities
Water treatment plants leverage these valves to manage the flow of water through filtration and treatment processes. Their durability and reliability are crucial for maintaining water quality standards.
4. Power Generation
In power plants, particularly those utilizing steam and high-pressure settings, these valves are essential for regulating steam flow and improving energy efficiency.
Choosing the Right Alloy Steel Instrumentation Ball Valve
When selecting an alloy steel instrumentation ball valve, it’s essential to consider various factors to ensure optimal performance. Here are key criteria to keep in mind:
- Pressure and Temperature Ratings: Ensure the valve is rated for the specific pressure and temperature conditions of your application.
- Size and Port Configuration: Choose the correct size and configuration to meet your operational requirements.
- Seal Material: Consider the seal materials based on the type of fluids passing through the valves, as this will impact longevity and durability.
- Actuation Methods: Determine whether manual or automated actuation is appropriate for your application.
- Certifications: Look for valves that meet relevant industry standards and certifications to ensure safety and reliability.
Installation and Maintenance of Alloy Steel Instrumentation Ball Valves
Proper installation and maintenance are critical to maximizing the lifespan and performance of alloy steel instrumentation ball valves. Follow these guidelines:
Installation
During installation, consider the following:
- Ensure the valve is compatible with the piping system, particularly regarding size and pressure ratings.
- Install the valve in a location that allows easy access for maintenance and operation.
- Verify the orientation of the valve; many ball valves can be installed in multiple orientations, but following manufacturer specifications is crucial.
Maintenance
Regular maintenance can help prevent major issues. Key maintenance practices include:
- Regular Inspections: Periodically check for signs of corrosion, wear, or leakage.
- Lubrication: Maintain the valve's operational efficiency with appropriate lubrication methods as recommended by the manufacturer.
- Test Functionality: Conduct routine tests to ensure the valve operates smoothly and seals properly.
- Replace Worn Parts: Proactively replace any worn or damaged components to prevent failures.
The Future of Alloy Steel Instrumentation Ball Valves
As industries continue to evolve and demand for enhanced efficiency and safety grows, the role of the alloy steel instrumentation ball valve will undoubtedly expand. Advancements in materials science and manufacturing technologies promise to yield even more durable, efficient, and versatile valve options in the future.
Moreover, with the rise of automation and smart technologies, we may see the integration of advanced monitoring and control systems within these valves, paving the way for greater precision and real-time data management. Companies that prioritize innovation in their valve offerings will lead the market, supporting sectors such as oil and gas, chemical processing, and power generation with high-quality solutions designed to meet modern challenges.
Conclusion
The alloy steel instrumentation ball valve is more than just a component; it is an essential part of efficient and safe industrial operations. Its durability, effectiveness in high-pressure applications, and adaptability across various sectors reinforce its status as a favorite among manufacturers and suppliers like Samvay Global. By understanding how to properly select, install, and maintain these valves, businesses can ensure their seamless integration into their systems, ultimately improving productivity and operational success.